After partnering with Kaleris to accelerate their yard operations, Bob Evans Farms reduced their loaded reefer hours by nearly 40% — that’s 134,000 hours. They also achieved estimated savings of over $471,000 in fuel and repairs and maintenance alone.
Bob Evans Farms' products have become a staple in most American homes and are ranked the #1 selling refrigerated side dishes in the United States. The company attributes its success to its unwavering focus on quality. This passion has guided the company for over 75 years, from its beginnings as a producer of premium farm-fresh sausage to its new broader mission of providing quick-to-table, farm-inspired dinner sides and breakfast items. Distribution was vital to the company's early success and has also been crucial to its longevity. Bob Evans Farms' dedicated supply chain operations team has continuously pursued improved efficiency and growth, striving to make their products available to more consumers nationwide.
The company's repeated investments in safety and efficiency are surpassed only by its desire to better serve its customers. Bob Evans Farms has grown from its beginnings as a small regional company based on its founder's farm in Southeastern Ohio to a national company with a sophisticated distribution network. Expansion requires scalability, and with today's rapid shifts in food production, Bob Evans Farms knew it needed to adapt again to sustain growth.
Bob Evans Farms, like many food & beverage manufacturers, must maintain the quality customers have come to expect. Losing an hour in the warehouse yard could spoil the product, elevating the need to have temperature-controlled trailers at the ready to preserve freshness. Because safety is the first of the company’s values, the team knew it was time to evaluate how technology solutions could help them avoid spoilage and stockouts, gain better control over product arrivals and departures, maintain a real-time view of trailer status and location, and meet tight delivery deadlines.
Bob Evans Farms searched for a solution that would fit the scale of its distribution facility, bringing with it operational advancements that propelled operations and drove new opportunities for success. It selected the Kaleris Yard Management System (YMS) to accelerate yard operations. YMS solutions have become increasingly present in food & beverage manufacturing, enabling providers to get their products out of the plant and into grocery stores quicker than ever before.
Kaleris, a provider of supply chain execution technology, partners with its customers to meet today’s expectations for shipper-to-grocer success with solutions tailored to food & beverage manufacturers. Its Yard Management System (YMS) optimizes operations, increases visibility and improves efficiency.
“By implementing a YMS and ensuring successful inventory at partnered stores, suppliers can become a shipper of choice and a trusted vendor for grocery stores,” said Kevin Humphrey, VP of Sales for Kaleris.
The implementation transformed the way Bob Evans Farms conducted day-to-day operations, helping minimize disruptions. The shift began with the real-time cargo visibility capability that makes tracking perishable goods in the yard as easy as checking the weather. It ensured timely deliveries, which in turn, helped Bob Evans Farms exceed food safety compliance policies. The addition of real-time tracking made pinpointing asset locations easier, which kept inventory loss to a minimum.
Bob Evans Farms’ journey to digitization and growth as a brand are prime examples of the reasoning behind technology adoption. Additionally, the team at Bob Evans Farms has improved coordination between yard staff, truck drivers, and other stakeholders, accelerating trailer movements and dock assignments. With a YMS in place, analog communications were replaced with a web portal that displayed asset availability. Yard assets, their location and their status are clearly visible. With recent innovations, Bob Evans Farms gained efficiency and more accuracy, reducing room for error and creating more potential for growth.
Bob Evans Farms runs a highly efficient supply chain operation at its Springfield, Ohio, location. Since its implementation in 2022, Kaleris YMS has made it possible for the team to achieve its goal of reducing the number of loaded trailers clogging up its network, reducing excess costs, and improving loaded trailer tracking.
Bob Evans Farms places its hardworking employees at the heart of the business. When employee safety is the most important aspect of a company, a well-equipped YMS goes a long way in boosting employee safety and efficiency in the yard. Employees can now locate team members operating vehicles at a moment’s notice with passive tracking and communicate via instant messaging, reducing congestion. This minimized the risk of accident and injury, and established a standardized process that better enforces safety protocols in the yard. The team can see and monitor everything from a centralized dashboard, enabling them to identify potential safety hazards, take proactive measures and mitigate risks.
With the YMS in place, decisions about yard activities are data-driven, leading to improved inventory allocation, trailer utilization, and resource planning.
One thing most retailers and food & beverage manufacturers have in common – with Bob Evans Farms as no exception – is the need to foster high customer satisfaction. Site-specific workflows prevent inventory loss and make sure grocers get what they care about most: products that arrive on time, in good, ready-to-eat condition for customers who’ve come to know and love the brand.
Many manufacturers with manual yard operations burn through their budgets in detention fees alone. With a reliable YMS, companies like Bob Evans Farms can capture all billable events, accessorial charges and charge accruals. It allows vendors to avoid unnecessary penalties and fees, creating what Bob Evans Farms is seeing in their yard today, a well-oiled machine that delivers on its promises as swiftly as it delivers its goods.
Sustainability is another important benchmark this year, and businesses must strive to meet their sustainable development goals to be a part of the solution. Bob Evans Farms saw fuel savings of over $470,000 in their first year with Kaleris YMS, significantly reducing their carbon footprint.
By optimizing trailer movements and reducing truck idling times, companies like Bob Evans Farms can further reduce fuel consumption and greenhouse gas emissions. Each sustainability contribution adds up, and a YMS helps food and beverage manufacturers make more sustainable use of resources over the years and minimize the need for additional infrastructure expansion by maximizing the utilization of existing resources.
Whether running multiple sites or managing a single distribution center, by automating its processes with a robust Yard Management System, manufacturers like Bob Evans Farms can future-proof their operations in a transformative way.
Holly Hall, Managing Director, MACH Alliance
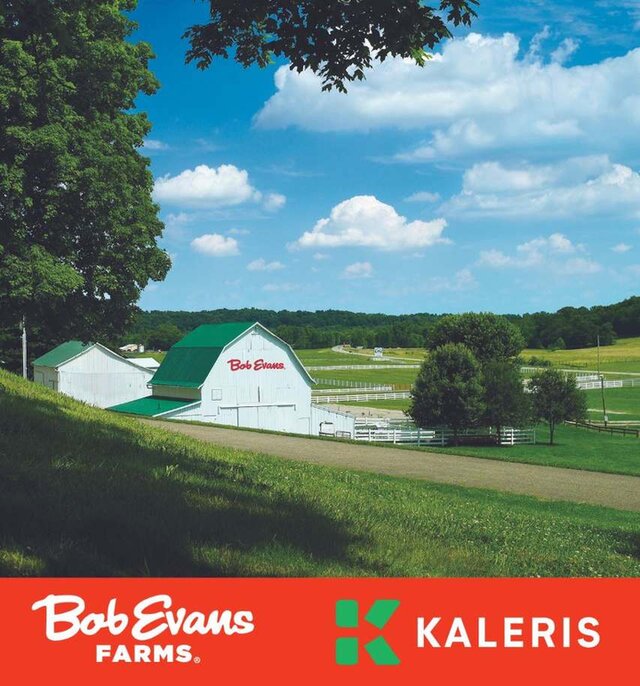
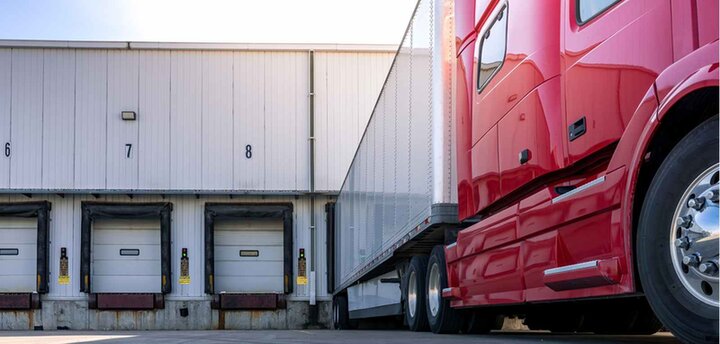
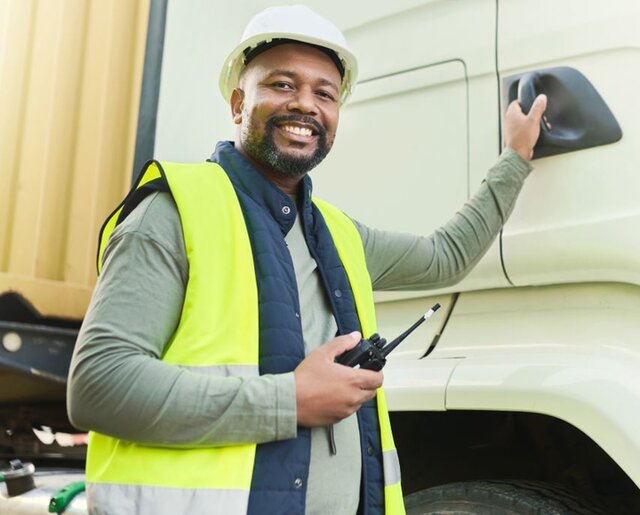
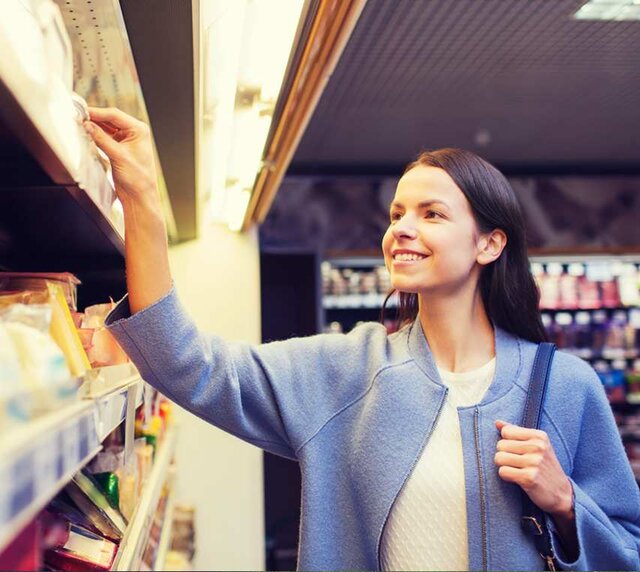
Investing in a Yard Management System
Transforming Yard Operations
Achieving Reduction Goals: Costs, Time, Fuel
Delivering Customer Satisfaction
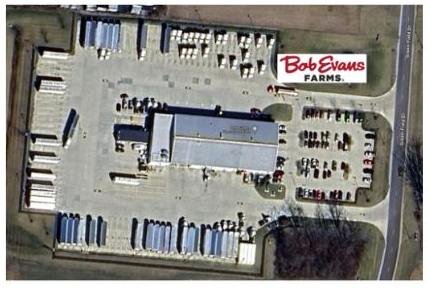